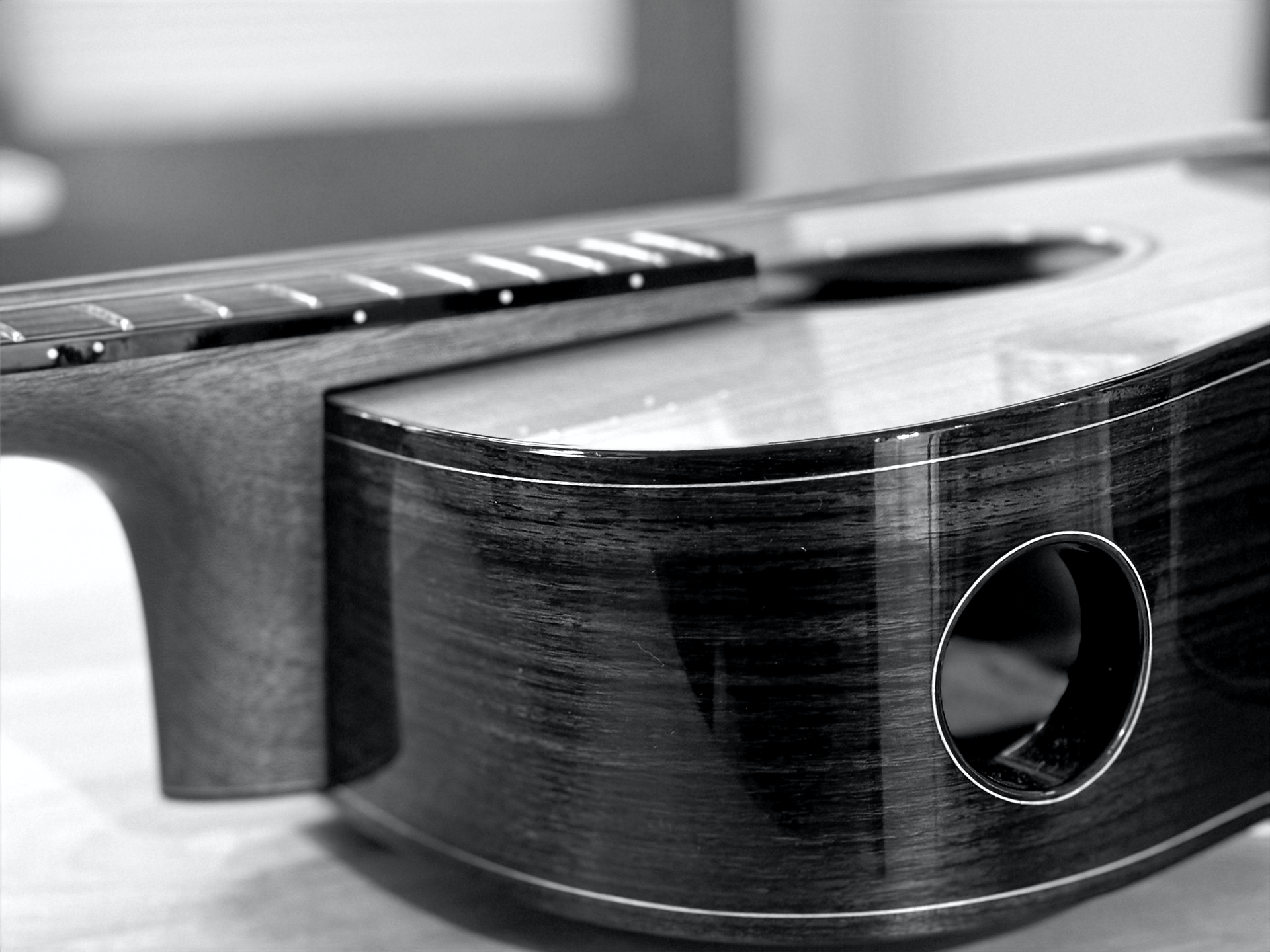
the guitar.

Lutherie, for me, is a way to practice craftsmanship in its most demanding form. Guitar making poses a unique set of challenges to the woodworker, challenges I find fascinating and, when met, extremely rewarding.
1.
The steel string acoustic guitar works best when constructed as light as possible so that it can respond to the energy of the strings while also being stiff enough to resist the crushing tension of those strings.
2.
It must be built with extreme accuracy to play in tune all over the fretboard.
3.
Its tone is shaped and colored through the use of different species of wood but it must be engineered to accommodate the various responses to environmental changes between those species.
4.
It must look beautiful, sound beautiful and be a joy to play.
I employ a number of construction techniques and design elements to create a timeless, responsive and sturdy instrument.
The back strap is an additional veneer of solid wood on the back of the peg head which extends onto the back of the neck to the third fret position. While beautiful and unique, it also serves a functional purpose by distributing the stress from the pull of the strings away from the peg head joint and reinforcing the joint against minor bumps. The veneer is carved so it blends seamlessly into the neck profile.
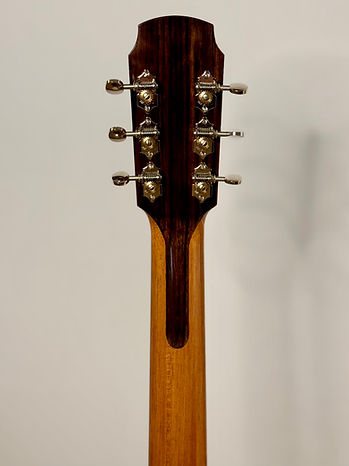

The floating fretboard extension solves a number of structural issues, some very long term, while also helping to shape the sound of the instrument.
Stress cracks, found in the tops of older instruments along the sides of the fretboard and arise primarily from the different responses to humidity between the dense fretboard and the soft guitar top, are eliminated by floating the fretboard over the guitar’s top much like on bowed instruments.
Furthermore, by extending the neck wood under the entire fretboard I find a noticeably even quality to the tone up and down the entire fretboard.
This method of construction also changes the attack angle of the strings at the saddle and lends a subtle warmth, a more rounded, sweeter tone to the instrument.
The side sound port is a favorite feature on my guitars. The opening in the upper bout on the bass side of the guitar allows the player to hear the instrument more clearly and accurately almost as if they are seated in front of the guitar. Inside the body, the area around the opening is laminated with two additional veneers with opposing grain directions to prevent stress cracks from forming and the opening is bound in matching lumber in order to seal any exposed end grain against humidity.


French Polish is the number one time-tested and proven finish for musical instruments. Not only does it impart a unique and beautiful luster to the instrument, it seals and protects the instrument with the least amount of dampening of the vibrating surfaces. There are plenty of very good guitars from large scale manufacturers that have been completely destroyed by thick, heavy synthetic finishes. The materials involved are completely eco friendly and the final result is totally repairable by any instrument maker experienced with the process. I mix my own shellac and make a fresh batch for each instrument. From start to finish, the polishing process takes more time than actually building the guitar but the clarity, in color and tone, are completely worth the effort.
Modal tuning is a method of measuring and tuning the frequency responses of the top plate, back plate and guitar box in order to shape the responsiveness of the guitar. It involves tapping the raw wood plates of the guitar and measuring the tones they produce with computer programs designed to analyze these frequencies. The charts produced by these programs are then used to determine the optimal plate thicknesses and bracing in order to create the most responsive instrument possible. These measurements are also taken from the completed guitar and, along with Chladni patterns, can be used to further tune and shape the responsiveness of the guitar. This exciting, new way to measure completed instruments and individual pieces of raw wood is just beginning to take hold among boutique builders and beyond the scope of mass production companies that need to build to an average response in order to meet large quotas.
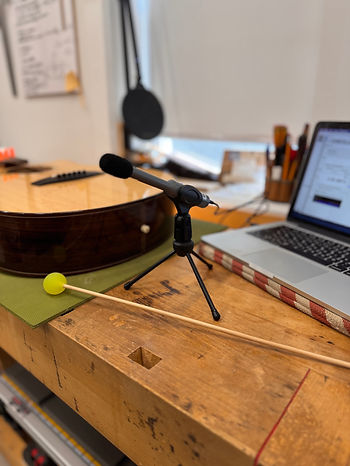
